What is Porosity in Welding: Comprehending Its Reasons and Enhancing Your Abilities
What is Porosity in Welding: Comprehending Its Reasons and Enhancing Your Abilities
Blog Article
Porosity in Welding: Identifying Common Issues and Implementing Finest Practices for Prevention
Porosity in welding is a prevalent problem that usually goes undetected till it creates significant problems with the integrity of welds. In this discussion, we will explore the key elements contributing to porosity formation, examine its detrimental effects on weld efficiency, and discuss the best techniques that can be taken on to decrease porosity event in welding procedures.
Typical Reasons of Porosity
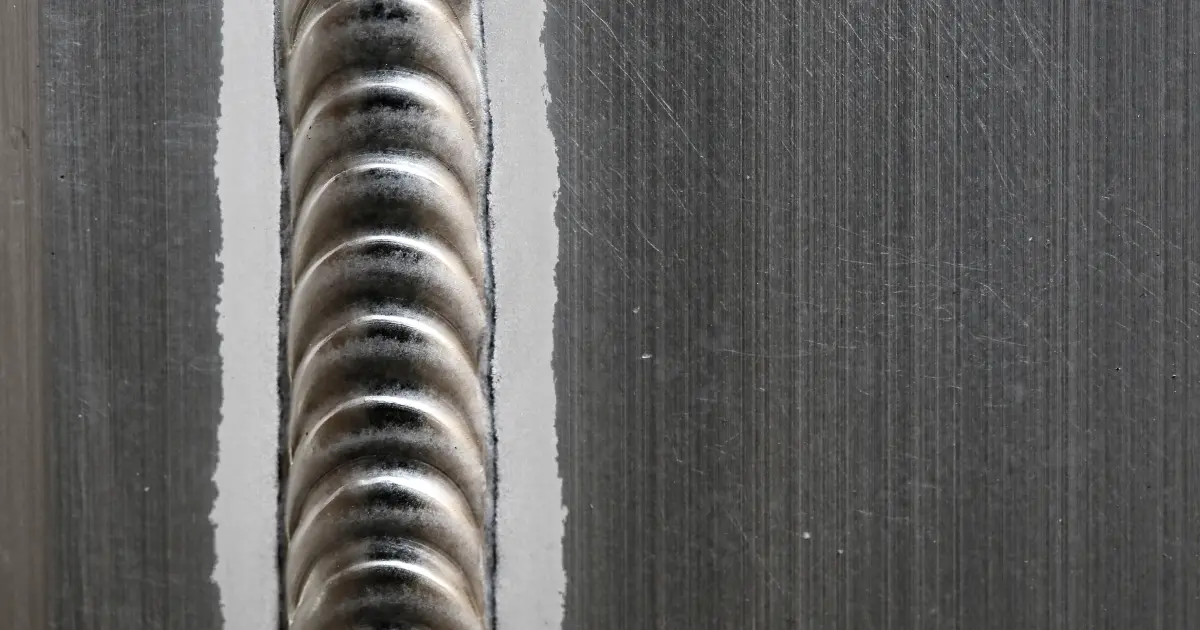
Using filthy or damp filler materials can introduce contaminations right into the weld, adding to porosity concerns. To mitigate these common reasons of porosity, thorough cleaning of base steels, correct securing gas option, and adherence to optimum welding criteria are necessary techniques in accomplishing top notch, porosity-free welds.
Effect of Porosity on Weld High Quality

The existence of porosity in welding can significantly jeopardize the architectural stability and mechanical residential or commercial properties of bonded joints. Porosity creates gaps within the weld metal, deteriorating its overall stamina and load-bearing capacity.
Welds with high porosity levels have a tendency to display reduced effect stamina and minimized capacity to flaw plastically prior to fracturing. Porosity can restrain the weld's capacity to properly send pressures, leading to early weld failing and prospective security dangers in important frameworks.
Finest Practices for Porosity Prevention
To enhance the structural integrity and top quality of bonded joints, what certain procedures can be carried out to lessen the incident of porosity during the welding procedure? Porosity avoidance in welding is vital to make sure the integrity and strength of the last weld. One efficient practice is proper cleansing of the base steel, removing any impurities such as rust, oil, paint, or moisture that can cause gas entrapment. Making sure that the welding devices remains in great condition, with tidy consumables and proper gas flow prices, can likewise significantly lower porosity. Furthermore, maintaining a steady arc and controlling the welding criteria, such as voltage, present, and take a trip speed, aids produce a consistent weld swimming pool that lessens the risk of gas entrapment. Making use of the appropriate welding strategy for the particular product being welded, such as readjusting the welding angle and gun setting, can further stop porosity. Regular assessment of welds and immediate remediation of any kind of issues determined throughout the welding process are crucial practices to stop porosity and produce top notch welds.
Importance of Proper Welding Techniques
Executing appropriate welding methods is critical in making sure the architectural honesty and top quality of bonded joints, constructing upon the structure of efficient porosity avoidance procedures. Welding methods directly impact the total toughness and durability of the bonded framework. One essential aspect of proper welding strategies is keeping the right warm input. Excessive heat can bring about raised porosity due to the entrapment of gases in the weld pool. Alternatively, inadequate heat might lead to incomplete blend, developing prospective powerlessness in the joint. In addition, utilizing the appropriate welding criteria, such as voltage, present, and travel rate, is essential for achieving sound welds with marginal porosity.
In addition, the choice of welding procedure, whether it be MIG, TIG, or stick welding, need to align with the certain requirements of the job to make certain optimal results. Appropriate cleansing and preparation of the base metal, in addition to picking the right filler material, are likewise crucial components of efficient welding strategies. By sticking to these best practices, welders can lessen the threat of porosity development and produce premium, structurally audio welds.

Examining and Quality Assurance Measures
Quality control steps play a vital i loved this duty in validating the honesty and integrity of bonded joints. Checking treatments are vital to detect and prevent porosity in welding, ensuring the strength and resilience of the final item. Non-destructive screening approaches dig this such as ultrasonic screening, radiographic testing, and visual inspection are generally used to determine prospective problems like porosity. These techniques enable the analysis of weld high quality without compromising the stability of the joint. What is Porosity.
Carrying out pre-weld and post-weld evaluations is also important in preserving quality control requirements. Pre-weld evaluations entail verifying the products, tools setups, and tidiness of the workspace to stop contamination. Post-weld inspections, on the various other hand, analyze the last weld for any type of problems, consisting of porosity, and confirm that it fulfills defined criteria. Executing a click here to find out more thorough quality assurance strategy that includes complete testing treatments and inspections is paramount to reducing porosity problems and making sure the total high quality of bonded joints.
Final Thought
To conclude, porosity in welding can be a common issue that influences the top quality of welds. By determining the common sources of porosity and implementing finest practices for avoidance, such as correct welding methods and testing actions, welders can make sure high quality and dependable welds. It is necessary to focus on prevention methods to decrease the incident of porosity and maintain the honesty of welded frameworks.
Report this page